Identifying fabrication-specific risks
Identifying fabrication-specific risks is a critical step in the risk assessment process during asset fabrication. These risks are unique to the fabrication phase and can impact the integrity, safety, and efficiency of the final asset. Identifying these risks early allows for proactive measures to mitigate them. Here are some common fabrication-specific risks to consider:
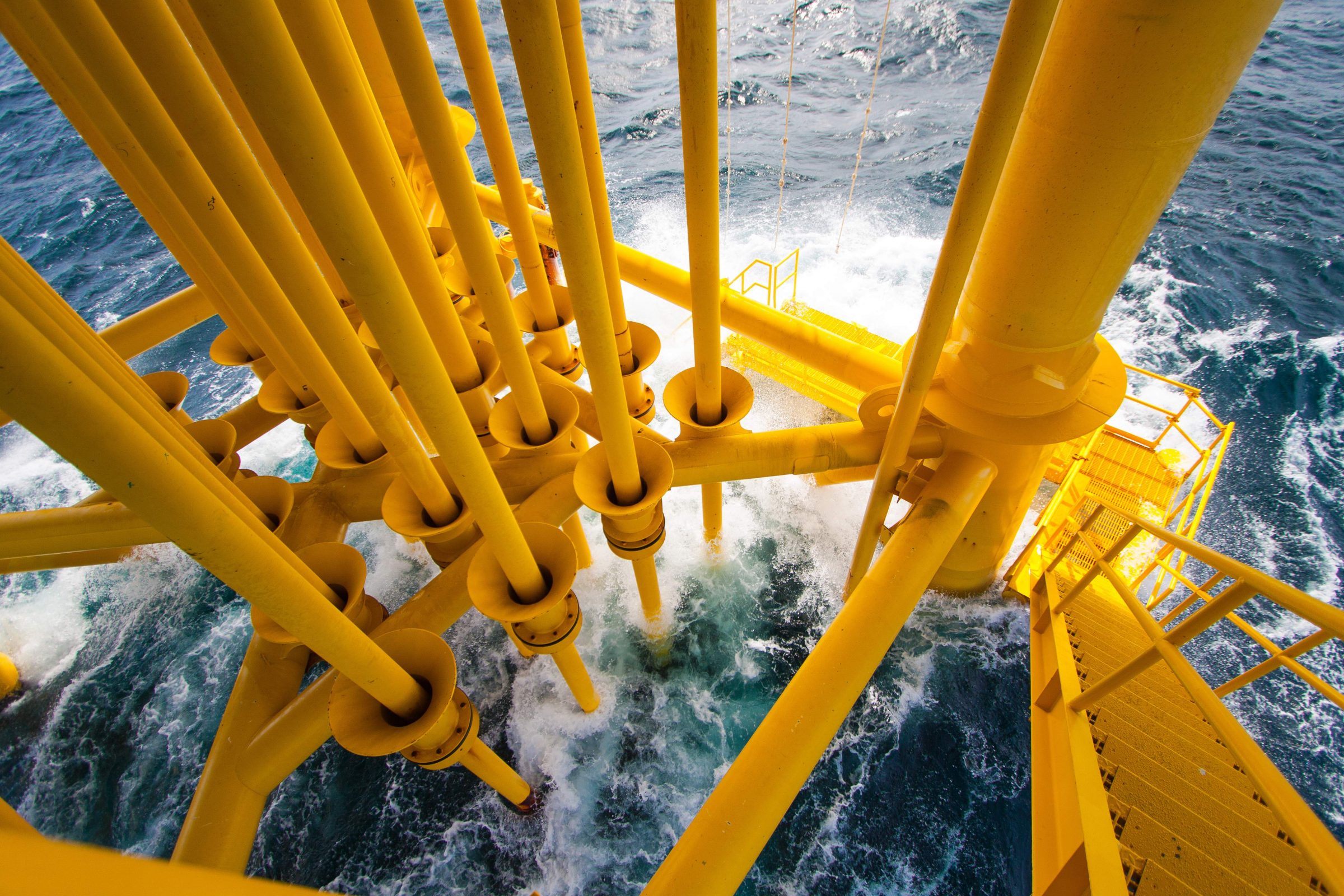
- Material Selection and Quality:
- Inadequate Material Quality: The use of substandard or counterfeit materials can compromise the structural integrity of fabricated components.
- Material Availability: Delays in sourcing or obtaining materials can lead to project schedule disruptions.
- Material Compatibility: Compatibility issues between different materials used in fabrication can result in corrosion or other compatibility-related problems.
- Welding and Joining Processes:
- Welding Defects: Welding processes may result in defects such as cracks, porosity, or incomplete fusion, impacting the structural integrity of welds.
- Improper Welding Procedures: Deviations from established welding procedures can lead to weaknesses in welded joints.
- Welder Qualification: Inadequately qualified or unskilled welders can produce subpar welds.
- Quality Control and Inspection:
- Inadequate Inspection: Insufficient or ineffective inspection and quality control processes can result in undetected defects or non-compliance with specifications.
- Lack of Documentation: Failure to maintain comprehensive records of inspections and quality control activities can lead to accountability issues.
- Safety Risks:
- Workplace Safety: Hazards related to working conditions, equipment, and tools can lead to accidents and injuries among fabrication workers.
- Hazardous Materials: The handling and use of hazardous materials, such as chemicals or flammable substances, pose safety risks.
- Environmental Risks:
- Emissions and Waste Management: Inadequate waste disposal practices or emissions control can result in environmental violations.
- Spill Risks: Accidental spills of chemicals or materials can have immediate environmental consequences.
- Schedule and Cost Risks:
- Project Delays: Delays in fabrication can lead to schedule overruns, impacting project timelines and budgets.
- Cost Overruns: Unforeseen issues or rework can lead to higher fabrication costs.
- Logistics and Transportation:
- Logistics Issues: Transportation delays, damaged components during transit, or improper handling during transportation can impact fabrication projects.
- Component Damage: Components may be susceptible to damage during loading, unloading, or transit, affecting their structural integrity.
- Regulatory Compliance:
- Non-Compliance: Failure to adhere to industry regulations and standards can result in legal and regulatory issues.
- Permitting and Licensing: Delays or issues related to obtaining necessary permits or licenses for fabrication activities.
- Resource Availability:
- Skilled Labor Shortages: Shortages of skilled labor, such as welders or fabricators, can impact project progress and quality.
- Equipment Availability: Unforeseen equipment breakdowns or shortages can cause delays.
- Documentation and Record Keeping:
- Incomplete Records: Poor documentation of fabrication processes, materials used, and inspections can lead to uncertainty and accountability issues.
It’s important to note that the specific risks in fabrication can vary widely depending on the nature of the project, the industry, and the location. Therefore, a comprehensive risk assessment process should involve a thorough review of project-specific factors and conditions to identify and prioritize these risks effectively. Additionally, engaging a multidisciplinary team with expertise in fabrication, materials, safety, and quality control is often essential for a robust risk identification process.