Principles and methods of NDT in fabrication
Non-Destructive Testing (NDT) is a group of inspection techniques used to assess the integrity, quality, and performance of materials, components, and structures without causing any damage or alteration to the tested items. NDT is crucial in various industries, including aerospace, automotive, construction, oil and gas, manufacturing, and more, where the structural integrity and safety of components are paramount. Here are some common NDT methods:
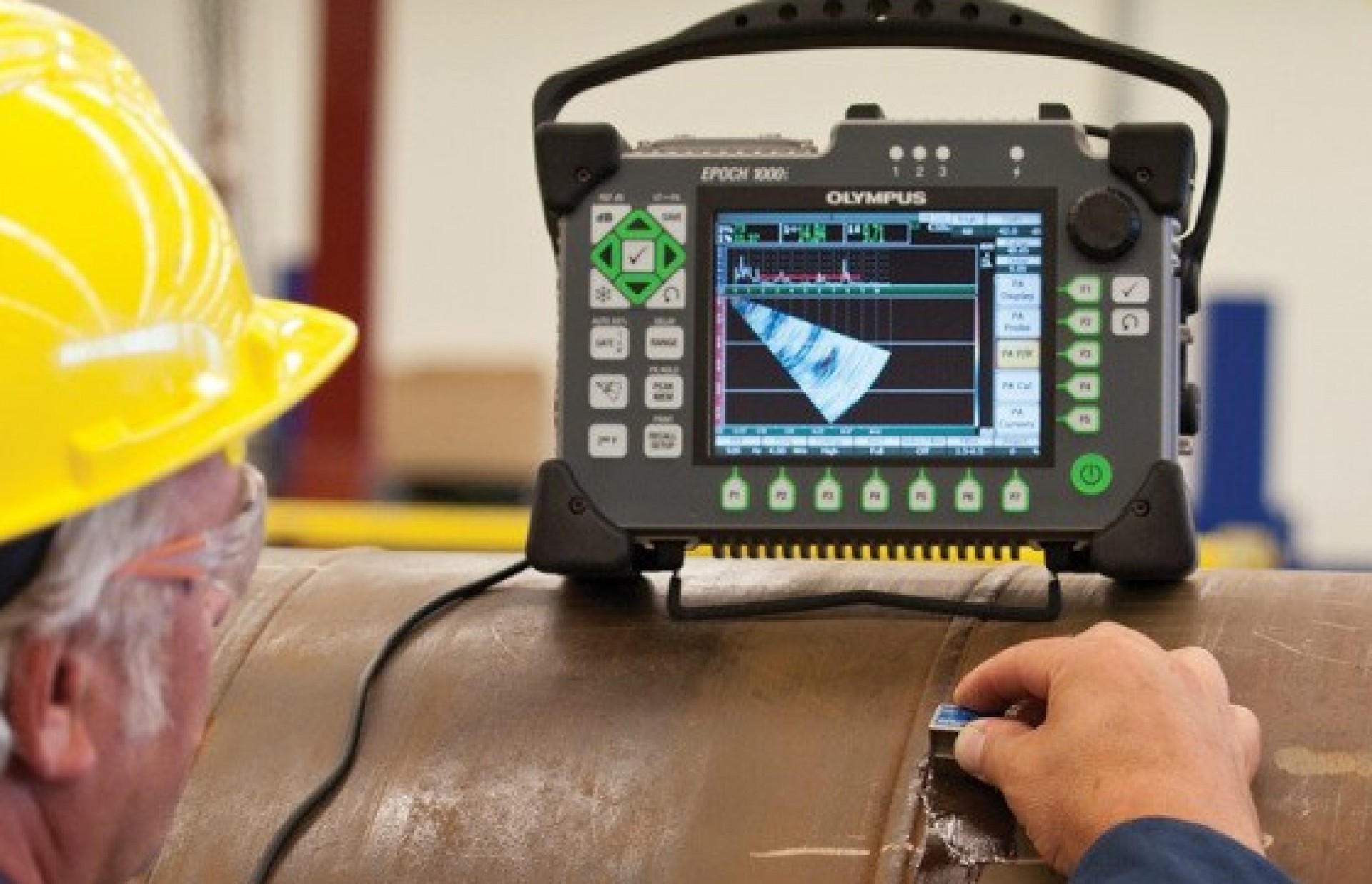
- Ultrasonic Testing (UT):
- UT uses high-frequency sound waves (ultrasound) to inspect materials for internal defects and thickness measurements.
- It detects defects such as cracks, voids, inclusions, and thickness variations.
- Radiographic Testing (RT):
- RT involves the use of X-rays or gamma rays to create images (radiographs) of the internal structure of a component.
- It is used to detect internal defects like voids, inclusions, cracks, and assess weld quality.
- Magnetic Particle Testing (MT):
- MT uses the principles of magnetism to identify surface and near-surface defects in ferrous materials.
- It’s effective for detecting cracks, weld discontinuities, and other surface defects.
- Dye Penetrant Testing (PT):
- PT involves applying a liquid dye penetrant to the surface of a component.
- The penetrant seeps into surface-breaking defects, and after excess penetrant is removed, a developer is applied to reveal defects like cracks and porosity.
- Eddy Current Testing (ECT):
- ECT uses electromagnetic induction to detect surface and subsurface defects in conductive materials.
- It’s often used for crack detection, material sorting, and conductivity measurements.
- Visual Testing (VT):
- VT is the simplest NDT method and involves a visual inspection of the component’s surface.
- Inspectors look for surface defects, discontinuities, and irregularities.
- Phased Array Ultrasonic Testing (PAUT):
- PAUT uses multiple ultrasonic elements to electronically steer and focus the ultrasound beam.
- It provides detailed and controllable inspections, often used for complex geometries.
- Time-of-Flight Diffraction (TOFD):
- TOFD uses ultrasonic waves to detect and size defects, typically cracks and weld discontinuities.
- It provides precise depth sizing of defects.
- Guided Wave Ultrasonic Testing (GWUT):
- GWUT employs low-frequency guided ultrasonic waves to inspect long lengths of pipes and structures.
- It’s used for corrosion detection and monitoring.
- Remote Visual Inspection (RVI):
- RVI involves the use of remote cameras or optical fibers to inspect areas that are difficult to access.
- It’s used for inspections within pipelines, tanks, or other confined spaces.
- Leak Testing:
- Various methods, including pressure testing and tracer gas testing, are used to detect leaks in pressurized systems.
- Acoustic Emission Testing (AET):
- AET monitors the acoustic emissions generated by materials when they are subjected to stress.
- It’s used for detecting active defects and monitoring structural health.
NDT plays a critical role in ensuring the safety, reliability, and quality of materials and structures. These methods are chosen based on the specific requirements of the inspection, the type of material being tested, and the nature of potential defects. Skilled NDT technicians and engineers interpret the results to make informed decisions about the suitability of components for service or the need for repairs.