Material Traceability
Material traceability is a critical aspect of quality control and assurance in various industries, including manufacturing, aerospace, automotive, healthcare, and construction. It involves tracking the origin, movement, and usage of materials throughout their lifecycle, from their source to their incorporation into finished products. Material traceability is essential for ensuring product quality, safety, compliance, and accountability. Here’s an in-depth look at material traceability:
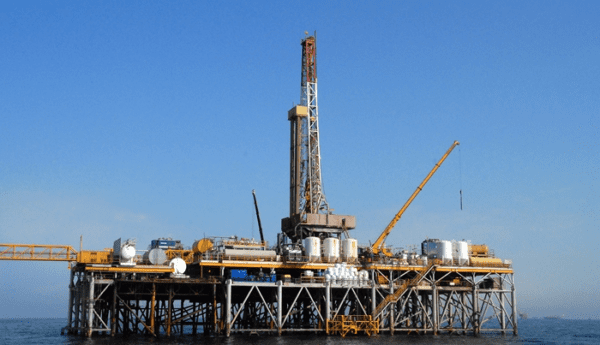
1. Why Material Traceability Matters:
- Quality Assurance: Material traceability helps ensure that materials used in manufacturing or construction meet specified quality standards and requirements.
- Regulatory Compliance: In regulated industries (e.g., aerospace, pharmaceuticals), traceability is often a legal requirement to demonstrate compliance with industry standards and regulations.
- Safety: Traceability can aid in identifying and recalling materials or products in case of safety concerns or defects, preventing potential hazards.
- Product Recalls: In the event of a product recall, traceability facilitates the identification of affected products and their source materials, minimizing risks and costs.
- Continuous Improvement: Traceability data can be used for analysis, identifying trends, and making data-driven decisions to improve processes and product quality.
2. Key Elements of Material Traceability:
- Material Identification: Assign unique identifiers to materials, such as serial numbers, barcodes, or RFID tags. These identifiers should be linked to comprehensive records.
- Documentation: Maintain detailed records of materials, including supplier information, certificates of compliance, test reports, and inspection records.
- Batch and Lot Control: Group materials with similar characteristics or production dates into batches or lots, allowing for easier tracking and management.
- Digital Systems: Leverage digital systems and software, such as Enterprise Resource Planning (ERP) or Manufacturing Execution Systems (MES), to streamline traceability processes.
3. The Traceability Process:
- Material Sourcing: Traceability begins with the identification of the source of materials, whether it’s raw materials, components, or sub-assemblies.
- Supplier Documentation: Require suppliers to provide documentation, including certificates of compliance and material test reports, that verify the quality and origin of materials.
- Receiving Inspection: Upon receipt of materials, conduct inspections and tests to ensure they match specified requirements.
- Material Handling: Implement proper handling and storage procedures to prevent contamination, damage, or deterioration of materials.
- Production Tracking: Monitor the movement and usage of materials throughout the manufacturing or construction process. Capture data at each production stage.
- Record Keeping: Maintain accurate and comprehensive records of all material-related activities, including transactions, inspections, and testing.
- Traceback Capability: Ensure the ability to trace materials back to their source and forward to their use in specific products or projects.
4. Technology and Automation:
- Utilize technology such as barcode scanners, RFID systems, and automated data capture to improve accuracy and efficiency in material tracking.
5. Auditing and Verification:
- Regularly audit and verify material traceability processes to ensure compliance with standards and regulations.
6. Reporting and Communication:
- Maintain open and clear communication about material traceability with relevant stakeholders, including customers, regulatory agencies, and auditors.
7. Continuous Improvement:
- Continuously assess and improve material traceability processes based on feedback, data analysis, and lessons learned.
Material traceability is a fundamental component of quality control and risk management. It not only ensures product quality but also helps organizations respond effectively to issues, enhance transparency, and build trust with customers and regulatory authorities.