Course Progress Bar
0% Complete
0/101 Steps
Course Navigation
Welding Techniques and Quality Control
Welding is a critical process used in various industries, including manufacturing, construction, aerospace, and automotive, to join materials together. Achieving high-quality welds is essential for ensuring the structural integrity, safety, and performance of welded components. Here’s an overview of common welding techniques and quality control measures:
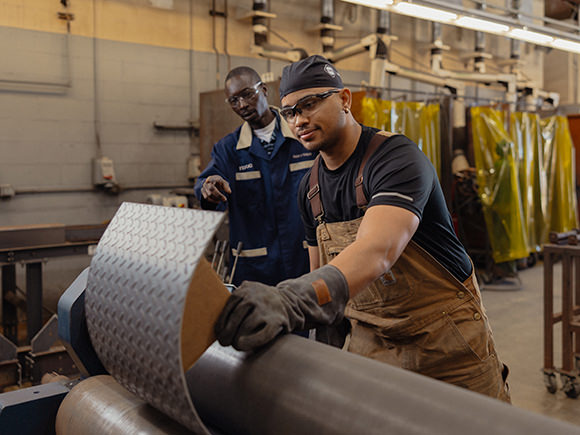
Common Welding Techniques:
- Arc Welding:
- Shielded Metal Arc Welding (SMAW): Also known as stick welding, SMAW uses a consumable electrode coated in flux. It’s versatile and widely used for various materials and applications.
- Gas Metal Arc Welding (GMAW): Also known as MIG (Metal Inert Gas) welding, GMAW uses a continuous wire electrode and shielding gas, making it suitable for high-speed, semi-automatic welding.
- Gas Tungsten Arc Welding (GTAW): Also known as TIG (Tungsten Inert Gas) welding, GTAW uses a non-consumable tungsten electrode and is prized for its precision and control.
- Resistance Welding:
- Spot Welding: Uses electrodes to join overlapping materials, commonly used in the automotive industry for sheet metal assembly.
- Projection Welding: Similar to spot welding but creates localized projections for stronger joints.
- Flash Butt Welding: Joins materials by creating an electrical arc and then forging them together.
- Solid-State Welding:
- Friction Welding: Joins materials by generating heat through friction and pressure, suitable for dissimilar materials.
- Ultrasonic Welding: Uses ultrasonic vibrations to create a solid-state bond in thermoplastic materials.
- Submerged Arc Welding (SAW): In SAW, an arc is formed beneath a layer of granular flux, providing excellent weld quality and high deposition rates, commonly used for heavy sections.
Quality Control Measures in Welding:
- Welder Qualification: Ensure that welders are certified and qualified for the specific welding process, materials, and positions they will work on.
- Welding Procedure Specification (WPS): Develop and document WPS that outlines the welding parameters, materials, and techniques to be used. Ensure compliance with industry standards and codes.
- Pre-Weld Inspection:
- Verify that materials are clean and free from contaminants.
- Ensure proper fit-up and alignment of the materials to be welded.
- Confirm the correct welding consumables are used.
- In-Process Monitoring:
- Use non-destructive testing methods like ultrasonic or radiographic testing to check for defects during welding.
- Monitor parameters such as voltage, current, and travel speed to maintain consistency.
- Post-Weld Inspection:
- Conduct visual inspections to check for weld discontinuities, such as cracks, porosity, and incomplete fusion.
- Employ destructive testing methods like tensile, bend, or hardness tests to evaluate the mechanical properties of welds.
- Welding Documentation:
- Maintain records of welding procedures, welder qualifications, inspection reports, and any corrective actions taken.
- Quality Assurance Programs:
- Implement quality assurance programs to ensure compliance with industry standards, codes, and regulations.
- Welding Equipment Maintenance:
- Regularly calibrate and maintain welding equipment to ensure consistent and accurate welds.
- Training and Certification:
- Provide ongoing training and certification for welders to keep their skills up to date.
- Corrective Actions: Implement corrective actions in response to non-conformities, and perform root cause analysis to prevent recurrence.
- Non-Destructive Testing (NDT): Utilize NDT methods such as radiography, ultrasonic testing, magnetic particle testing, and dye penetrant testing to identify internal defects in welds without causing damage.
- Welding Procedure Qualification: Conduct tests to qualify welding procedures, ensuring they meet the required standards and codes.
- Visual Inspection: Perform visual inspections to check for surface defects, such as weld spatter, undercut, and incomplete penetration.
Quality control in welding is vital to ensure the reliability and safety of welded components. Adhering to industry standards, employing skilled welders, and implementing thorough inspection and testing processes are key elements in achieving high-quality welds.